What Materials Are Needed for Screen Print Transfers?
- Screenprint direct
- Aug 23, 2024
- 3 min read
Screen print transfers are a popular choice for creating custom apparel, allowing for vibrant designs that can be easily applied to various fabrics. Whether you're a seasoned screen printer or a beginner, understanding the essential materials needed for this process is crucial to achieving high-quality results. In this blog, we'll explore the key materials required for screen print transfers.
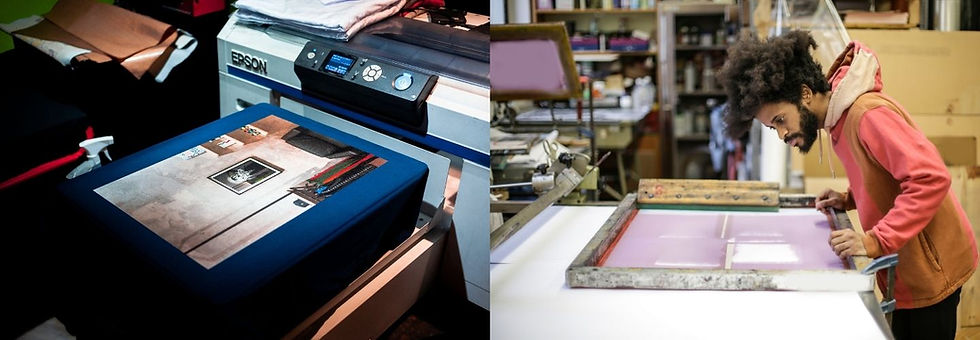
1. Transfer Paper
Transfer paper is the foundation of screen print transfers. It’s a special type of paper that holds the ink or toner, which is later transferred onto the fabric. Two main types of transfer paper are commonly used:
Hot Peel Transfer Paper: Ideal for vibrant and detailed designs, this type of paper allows the design to be peeled off immediately after pressing.
Cold Peel Transfer Paper: Offers a more matte finish and requires the design to cool before peeling.
2. Screen Printing Ink
The quality of your screen print transfer largely depends on the ink you use. There are different types of inks suited for various purposes:
Plastisol Ink: A popular choice due to its vibrant colors and durability. It sits on top of the fabric, creating a slightly raised texture.
Water-Based Ink: Ideal for a softer feel and eco-friendliness. This ink soaks into the fabric, making it less noticeable to the touch.
Discharge Ink: Used for achieving soft prints on dark fabrics by removing the dye from the fabric and replacing it with ink.
3. Screen Printing Screens
Screens are used to hold the stencil of your design. The type of mesh you choose affects the detail and quality of your transfer:
110 Mesh: Best for basic designs with bold lines and large details.
230 Mesh: Suitable for more intricate designs with fine details.
4. Squeegee
A squeegee is essential for pushing the ink through the screen and onto the transfer paper. The squeegee should be firm enough to apply even pressure but flexible enough to adapt to the screen's surface.
Firmness: Harder squeegees are ideal for fine details, while softer ones are better for large, solid areas.
Size: The width of the squeegee should match the size of your design to ensure even ink distribution.
5. Heat Press
A heat press is used to transfer the design from the transfer paper onto the fabric. The right temperature, pressure, and timing are crucial to ensuring a successful transfer.
Temperature Settings: Different fabrics require different heat settings. For example, cotton typically requires a higher temperature than polyester.
Pressure Settings: Consistent pressure is necessary to ensure the design adheres properly to the fabric.
Timing: The duration for which the heat press is applied also varies depending on the type of ink and transfer paper used.
6. Release Powder (Optional)
Release powder can be used to improve the adhesion of the transfer to the fabric. It’s especially useful when working with intricate designs or when extra durability is needed.
7. Adhesive Powder (Optional)
Adhesive powder helps the ink stick better to the transfer paper, ensuring a cleaner and more detailed print.
8. Teflon Sheets
Teflon sheets are placed over the transfer during the heat press process to prevent the ink from sticking to the heat press and to ensure an even heat distribution.
Conclusion
Creating screen print transfers requires a specific set of materials, each playing a crucial role in the final outcome of your design. By choosing the right materials and understanding their purpose, you can produce high-quality transfers that will look great on any fabric. Whether you're creating custom t-shirts, bags, or other apparel, having the right materials on hand is the first step to success in screen printing.
Comments